Are you ready for the Industry 4.0?
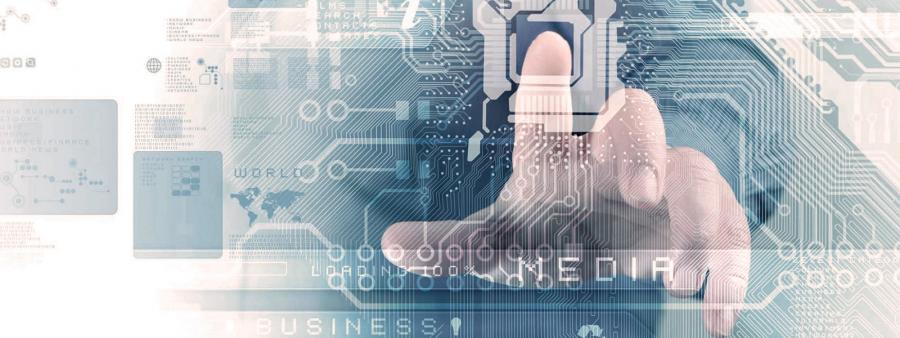
When we talk about Digital Transformation of the Companies, we talk about all the business opportunities that have appeared in the last years thanks to the adoption of new technology. Concretely, if we have to think about sectors that could be benefited by the introduction of, for example, the Internet of Things or Big Data to the business, this sector would be the Industry. Nonetheless, at the same time, thinking about Industry sector, this leads to a traditional way of working.
The introduction of technologies to the industrial companies can have a great impact in the production, logistics, sales and research & development areas. The reality is that the majority of the companies from the industrial sector are not prepared for this change. At European level, around 75% of managers are not sufficiently well skilled on the new paradigm of Industry 4.0. However, before analysing how to change this situation, let us introduce you briefly, what is Industry 4.0, the description of one of the main challenges for Industry 4.0 and the most outstanding technologies associated to face it.
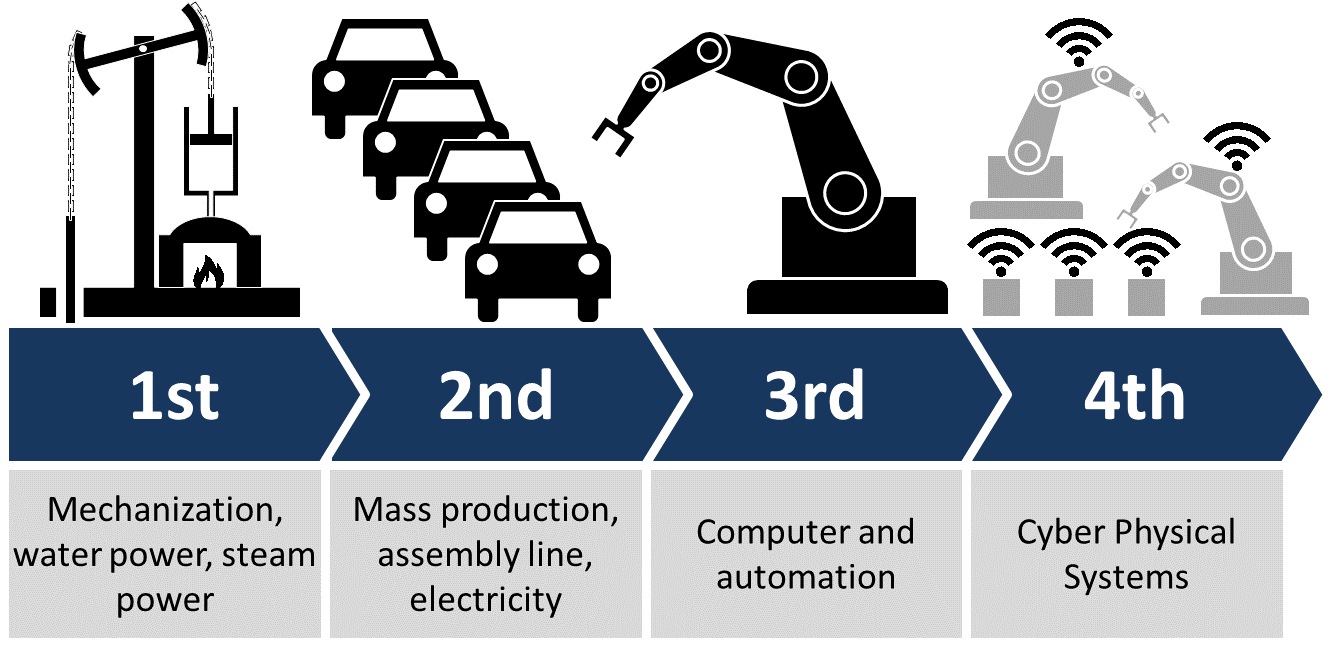
Industrial Revolutions (Image from: Christoph Roser at AllAboutLean.com (CC))
Technologies like Cloud Computing, Internet of Things, Robotics, Big Data, Machine Learning, Artificial Intelligence or Automation are commonplace in Tech Companies. Industry 4.0, also known as 4th Industrial Revolution, is the adoption of these new generation technologies and systems to its plant productions and its business.
One of the most common use cases from the traditional industry is a fabrication plant. There, employees and machines work together in a line in order to produce or maintain a whole product or a part of it. Usually, these plants are not dynamic and it is hard to introduce changes. If there is a malfunction/problem in the chain, it has to be a static validation process (by a worker or a specific machine), meaning that it could be defective products produced before the failure is detected. The main problem of this connectionless plant are, for example, the flexibility and the offline control. Since the moment that there is no automated tracking of the line, it is not possible to control what is happening to the components of the product in an analytical way.
Indeed, data and their management play a crucial role on the digital transformation path toward Industry 4.0. Typically, the aforementioned IoT domains are composed by several devices that generate continuous data flows (also referred to as data streams). When all these data streams are put together to integrate them, it becomes unfeasible to use traditional data management techniques to analyse them due to their lack of scalability and inability to quickly provide reliable results from large data sets. Therefore, this 4th industrial revolution can take advantage of the recent advances in the Big Data domain concerning storage, computation, and analytics. This might enable practitioners to (1) store vast amounts of data using cloud storage infrastructures (either public, private or hybrid), (2) boost the performance of the data collection and retrieval operations, and (3) run powerful distributed data analytics algorithms over these data in a cost affordable and on-demand way.
Overall, this (big) data layer is committed to provide a new dimension to all industry stakeholders and contribute to a more flexible adaptability of the industry to new market needs and production process while optimizing the available resources.
Novel and more adaptable data management and visualization systems are used in order to tackle with the huge amount of information that can be generated in real-time by IoT infrastructures. These systems, often in the form of new generation SCADAs or IoT Cloud platforms allow industrial managers to have a much more exhaustive control of what is happening in their business, not only in production line or logistic phase but even after selling the product for maintenance and post-sales purposes. Moreover, besides the real-time control monitoring of products, tools, machines and workers, as said previously these new systems allow to store great amounts of data that can be used for better future business planning adjusting the production to data-oriented decisions based on previous patterns.
However, all these information and automation systems can lead also to new threads and risks related to cybersecurity aspects. Actually, going through this industry digital transformation and integrating those practices without taking into account security aspects properly could cause eventually more losses than benefits. Cybersecurity is not an option, is a must in the equation.
As mentioned above, Industry 4.0 takes advantage of the introduction of new technologies to create intelligent industrial manufacturing processes that demand high connectivity between its components without renouncing to basic requirements of business continuity and high availability. This fact leads to the implementation of more open and interconnected Industrial Control Systems to take full advantage of these technologies, leading to greater exposure to security threats, both traditional and targeted at specific components of the industrial sector (f.e SCADA systems). Although the mentioned technologies have been widely used in the ICT world, they have had a low implantation in the industrial sector up to now and pose new security challenges. We can see the industry as a Cyber Physical System full of sensors and control elements capable of connecting machines and devices with plants, fleets, networks and human beings. To protect these systems and processes of Industry 4.0 is essential to take into account that it will be necessary to ensure; (1) the availability of facilities, manufacturing processes and Cyber Physical Systems, (2) the integrity of processes and configurations of field devices and, industrial networks and their communication with industry-specific protocols, and (3) the confidentiality of the information and data handled. In addition, given that these new industrial systems must provide ubiquity, remote access and autonomous behaviour, there is a concern that data and information are only accessible by authorized persons or to protect intellectual property/know-how of companies. Then, it is relevant to have a correct access control to the systems, data and processes of the new Industry 4.0.
With all this, at the end, the key point of the Industry 4.0 is the culture of the company, where are the workers who are going to interact with the renewed information and management systems. In this new paradigm, employees are the most important part of the value chain, moving from a line-centred view to a worker-centred view. This means that the worker has the power to stop the production line or to introduce changes in the processes with the aim of introducing continuous improvements. The old defined processes need to be modified in order to achieve the new goals of the organization.
That is why we need to prepare workers for this brand new way of working in an old-fashioned industry with the objective of changing it. During the months of June, July and September, the European Erasmus+ Project, SPRINT 4.0 is going to host different one-week courses focusing on the aforementioned issues and tech solutions for this new challenging paradigm, working in interdisciplinary teams, with the final objective of solving a real challenge from a company of the project.
These courses are:
- Production system automation (Pisa) hosted by Universitá di Pisa (UniPi)
- Data and Security (Barcelona) hosted by La Salle – Ramon Llull University
- Industrial IoT (Bremen) hosted by Bremer Institut für Produktion und Logistik GmbH (BIBA)
The other companies involved in the project are Intooition, TOI SRL, Fundazione Giacomo Brodolini, Selettra, OHS Engineering and Celsa Group.
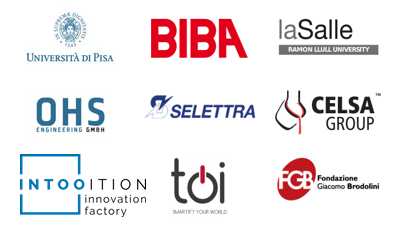
SPRINT 4.0 Partners
All interested parties will participate in different workshops to analyse Industry 4.0 solutions, based on the idea of co-creation, focused on 'Learning by doing' and methodologies of learning about problems and their implementation in a multidisciplinary environment. At the end of each course, a prEtotype competition will be opened during 1 month, asking for a solution for the specific challenge presented during the course. The students’ team winning the prEtotype competition will have the possibility of experience a 30 days transnational mobility within one of the partner company.
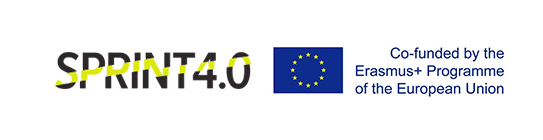